Table of Contents
Introduction
In the ever-evolving landscape of modern manufacturing, the role of custom metal fabrication has become increasingly pivotal. As industries across the spectrum – from aerospace and automotive to construction and renewable energy – strive for greater efficiency, quality, and innovation, the demand for expertly crafted, precision-engineered metal components has soared.
At the heart of this transformation lies the skilled practice of custom metal fabrication, a multifaceted craft that seamlessly blends the art of metalworking with the precision of advanced technologies. At [Company Name], we have witnessed firsthand the transformative power of this specialized field, and in this comprehensive blog post, we will delve into the myriad ways in which custom metal fabrication is revolutionizing modern manufacturing.
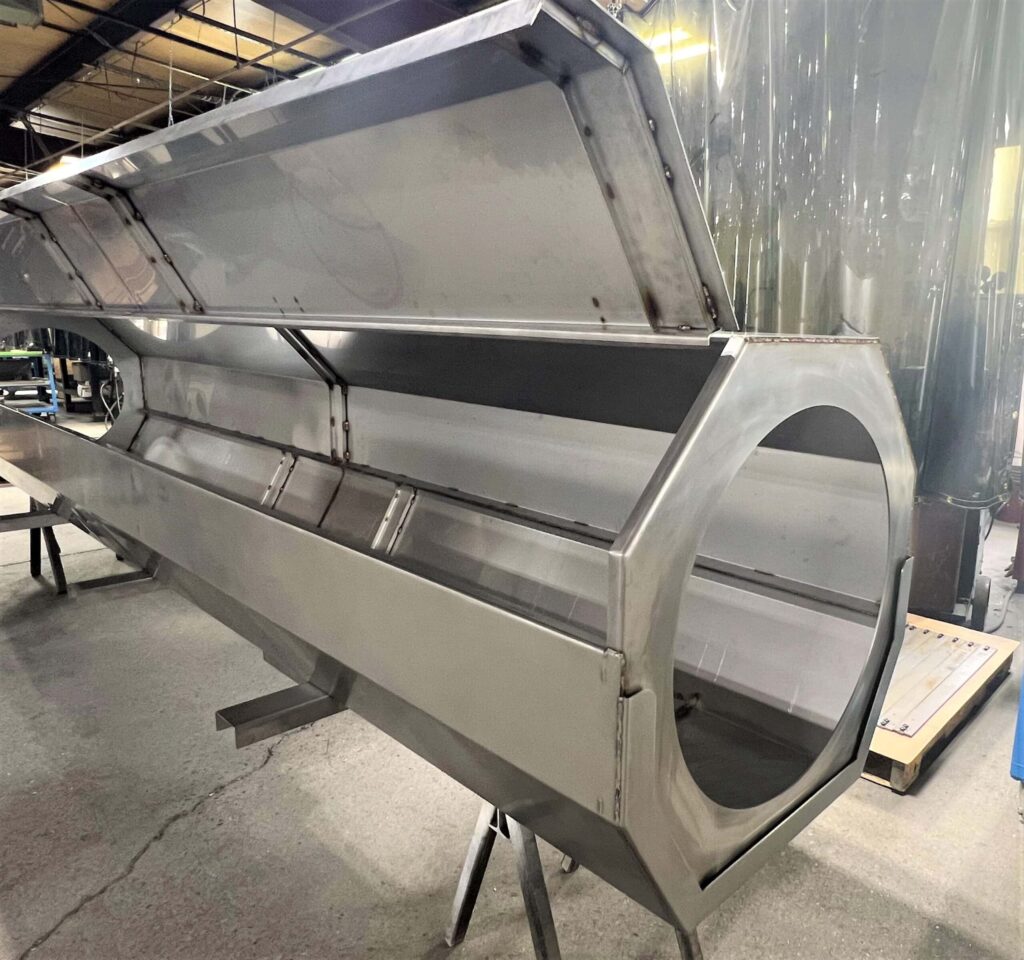
The Rise of Custom Metal Fabrication: Driving Efficiency and Innovation
Custom metal fabrication has emerged as a critical enabler of modern manufacturing, providing a versatile and adaptable solution to the evolving needs of industries. Unlike mass-produced, off-the-shelf components, custom-fabricated metal parts are precisely engineered to meet the unique specifications and requirements of each project, ensuring a perfect fit and optimal performance.
One of the key advantages of custom metal fabrication lies in its ability to enhance efficiency and cost-effectiveness. By working closely with clients to understand their specific needs, fabricators can design and produce parts that are tailored to the intended application, minimizing waste, reducing lead times, and optimizing material utilization. This, in turn, translates into significant cost savings for manufacturers, allowing them to remain competitive in an increasingly dynamic market.
Moreover, the flexibility inherent in custom metal fabrication empowers manufacturers to adapt to changing market demands and technological advancements. Through the strategic use of advanced tools and techniques, such as computer-numerical control (CNC) machining, welding, and metal forming, fabricators can rapidly prototype, iterate, and manufacture specialized components that drive innovation and give their clients a competitive edge.
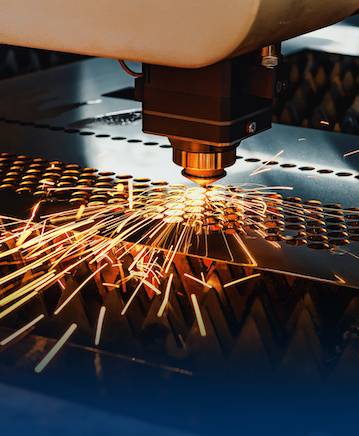
Leveraging Cutting-Edge Technologies: The Synergy of Craftsmanship and Innovation
At the heart of the custom metal fabrication process lies the seamless integration of expert craftsmanship and cutting-edge technologies. By harnessing the power of Computer Numerical Control (CNC) machining, metal forming techniques, and state-of-the-art welding capabilities, fabricators are able to produce metal components that are not only visually stunning but also engineered to the highest standards of quality and precision.
CNC machining, for example, has revolutionized the way metal parts are manufactured. This advanced technology allows for the precise, computer-controlled shaping and cutting of metal, enabling fabricators to create intricate designs, tight tolerances, and complex geometries with unparalleled accuracy. The integration of CNC machining into the custom metal fabrication process has significantly improved the efficiency, consistency, and repeatability of part production, ensuring that each component meets the most stringent requirements.
In addition to CNC machining, custom metal fabrication also leverages specialized metal forming techniques, such as bending, stamping, and punching, to transform raw materials into sophisticated, three-dimensional structures. These processes, combined with the expertise of skilled fabricators, enable the creation of highly complex, ergonomic, and aesthetically pleasing metal parts that seamlessly integrate into a wide range of applications.
Furthermore, the use of advanced welding technologies, including MIG, TIG, and robotic welding, has become integral to the custom metal fabrication process. By employing these state-of-the-art techniques, fabricators can produce strong, durable, and visually appealing welds that meet the most demanding industry standards. This level of precision and attention to detail is essential in ensuring the structural integrity and long-term performance of custom-fabricated metal components.
Unlocking Design Flexibility: Empowering Manufacturers to Innovate
One of the most transformative aspects of custom metal fabrication is its ability to unlock unparalleled design flexibility for manufacturers. Unlike mass-produced, off-the-shelf components, custom-fabricated metal parts are engineered to meet the specific requirements of each project, allowing for the exploration of innovative design concepts and the incorporation of unique features that can drive industry-wide advancements.
By working closely with clients, custom metal fabricators can translate even the most complex and intricate design ideas into tangible, high-quality metal components. This level of design flexibility empowers manufacturers to push the boundaries of what is possible, enabling them to create products that are not only visually stunning but also highly functional and tailored to their specific needs.
Moreover, the versatility of custom metal fabrication allows manufacturers to adapt to evolving market trends and technological advancements. As industries continue to innovate and evolve, the ability to quickly prototype, refine, and produce custom-engineered metal parts becomes increasingly crucial. Custom metal fabricators, with their agile and responsive approach, are well-positioned to support manufacturers in their pursuit of innovation, helping them to stay ahead of the curve and maintain a competitive edge.
Quality and Durability: The Hallmarks of Custom Metal Fabrication
At the heart of custom metal fabrication lies an unwavering commitment to quality and durability. Unlike mass-produced parts, custom-fabricated metal components are engineered and manufactured with the utmost attention to detail, ensuring that they not only meet but exceed the most stringent industry standards.
Throughout the custom metal fabrication process, a comprehensive quality control system is meticulously implemented to ensure the consistent production of high-quality parts. This includes thorough inspections at every stage of the fabrication process, from material selection and cutting to welding and finishing. By employing advanced measurement tools and techniques, fabricators can maintain tight tolerances, minimize defects, and guarantee the structural integrity and long-term performance of the final product.
Moreover, the use of premium-grade materials and the application of specialized finishing techniques, such as powder coating, anodizing, and plating, further enhance the durability and corrosion resistance of custom-fabricated metal components. This attention to detail not only extends the lifespan of the parts but also ensures that they can withstand the rigors of demanding industrial environments, from harsh weather conditions to heavy-duty usage.
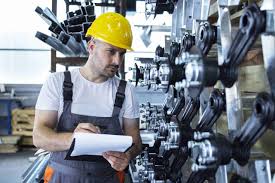
Industry Applications: Revolutionizing Diverse Sectors
The transformative power of custom metal fabrication extends far beyond a single industry; it is a versatile and invaluable resource that is revolutionizing a wide array of sectors, from aerospace and automotive to construction and renewable energy.
In the aerospace industry, for example, custom metal fabrication plays a crucial role in the production of intricate, high-precision components that are critical to the performance and safety of aircraft. By leveraging advanced manufacturing techniques, such as CNC machining and specialized welding, fabricators can create complex metal parts that meet the stringent requirements of this highly regulated sector, ensuring the reliability and longevity of these mission-critical components.
Similarly, in the automotive industry, custom metal fabrication is instrumental in the development of innovative vehicle designs and the production of specialized parts. From custom-fabricated body panels and structural components to bespoke engine and suspension parts, the flexibility and precision of this craft enable manufacturers to push the boundaries of automotive engineering, creating vehicles that are not only visually appealing but also highly functional and durable.
Beyond these industries, custom metal fabrication is also making its mark in the construction and renewable energy sectors. In the construction industry, fabricators are producing custom-engineered metal components, such as architectural features, structural supports, and specialized equipment, that are enabling the realization of innovative and ambitious building designs. Meanwhile, in the renewable energy sector, custom metal fabrication is contributing to the development of advanced solar panels, wind turbine components, and other clean energy solutions, helping to drive the global transition towards a more sustainable future.
What are the key benefits of custom metal fabrication for modern manufacturing?
Increased flexibility and adaptability to changing market demands
Enhanced precision and quality of final products
Improved efficiency and cost-effectiveness in the manufacturing process
Personalized solutions that cater to specific customer requirements
Scalability and capacity to handle projects of varying scales
How can custom metal fabrication help businesses stay competitive in the modern manufacturing landscape?
Enables quick response to evolving market conditions and customer needs
Delivers high-quality, customized products that differentiate businesses
Optimizes the manufacturing process for improved efficiency and cost-effectiveness
Provides scalable solutions to adapt to changing production demands
Leverages the latest technologies and industry expertise for a competitive edge
What industries can benefit from the services of a custom metal fabricator like CNFabricators?
Renewable energy
Industrial equipment
Architecture and construction
Transportation and logistics
And many other industries that require specialized, high-quality metal components and assemblies
How can businesses get started with custom metal fabrication services from CNFabricators?
1. Reach out to the CNFabricators team to discuss your specific requirements and manufacturing needs
2. Collaborate with the in-house engineering and design experts to optimize the fabrication process
3. Leverage the comprehensive range of fabrication services to create tailored solutions
4. Enjoy the benefits of working with a trusted, industry-leading custom metal fabricator
Conclusion: The Future of Custom Metal Fabrication
As the manufacturing landscape continues to evolve, the role of custom metal fabrication has become increasingly pivotal. This specialized craft, which seamlessly blends expert craftsmanship with the power of advanced technologies, is revolutionizing the way industries approach design, production, and innovation.
Through its ability to deliver precision-engineered, custom-fabricated metal components that meet the unique requirements of each project, custom metal fabrication is empowering manufacturers to push the boundaries of what is possible. By unlocking design flexibility, enhancing efficiency, and ensuring the production of high-quality, durable parts, this specialized field is poised to play an ever-more-crucial role in the future of modern manufacturing.
As industries across the spectrum continue to evolve and innovate, the demand for the expertise and versatility offered by custom metal fabrication will only continue to grow. At [Company Name], we are committed to staying at the forefront of this dynamic field, constantly exploring new technologies, refining our processes, and collaborating with our clients to deliver solutions that drive progress and inspire the next generation of industry leaders.
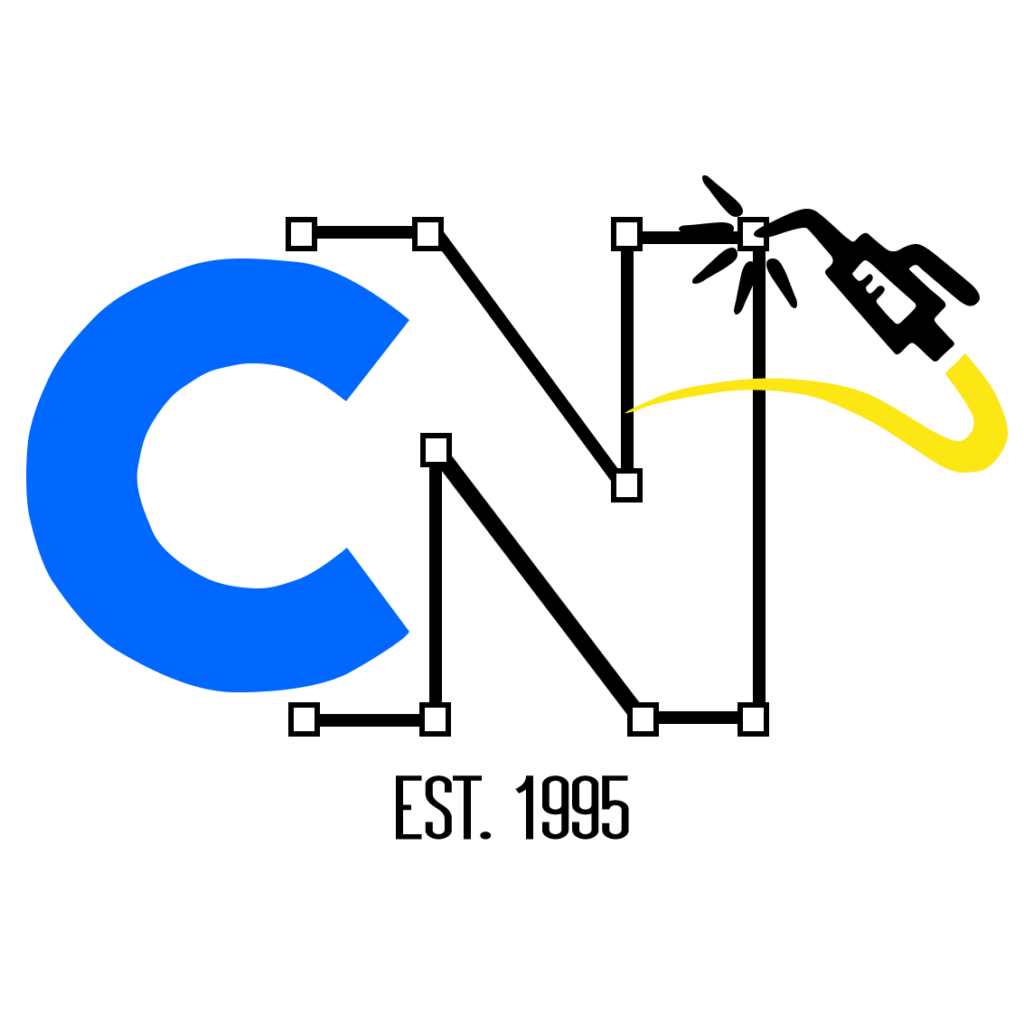